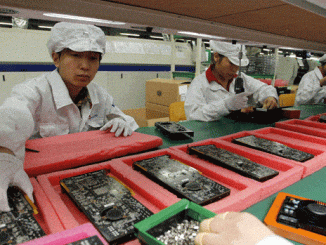
What is Operational Excellence?
Operational Excellence is about understanding what you do, how you do it, your purpose, and the value you bring as a stakeholder to your organization.
We’ve summarized the three key points needed in every operational excellence guide, whether it be Lean Six Sigma based or BPM, business process management based.
1. Consistently develop, deliver, and maintain defect-free products and services to our customers as quickly and efficiently as possible
2. Should defects occur, or defective product or services be delivered, we will strive to understand the causes of variation and eliminate them steadfastly so they never occur again. We promise to learn from our mistakes
3. We will strive in order to understand causes of variation and do what we can in our power and control to prevent defects from occurring
In order to do so you’ll need a common language, common tools, and collaborative team work to streamline and replicate our success to now and going forward. It’s important to remember that the way we’ve been doing things for the past several years is not necessarily the best way to bring your colleagues to the next level of achievement.
We also need a common language to interact with our suppliers and customers. It’s important to highlight that what our customers consider as defective or of poor quality be agreed upon by yourself as well as your partners. Your processes, products, and services must be designed or tailored in such a way as to identify causes for variation and subsequent action to be taken.
While Operational Excellence doesn’t dictate how your job should be done, it does provide the tools and guidance should you be faced with challenges that prevent you from delivering your product or service on time to the customer and according to our customers’ requirements.
Think your opex guide as a large toolbox filled with the tools to tackle just about every problem you’ll encounter. The more you consult the guide and apply the principles, the more you’ll be able to apply the right tool, at the right time.
Be the first to comment