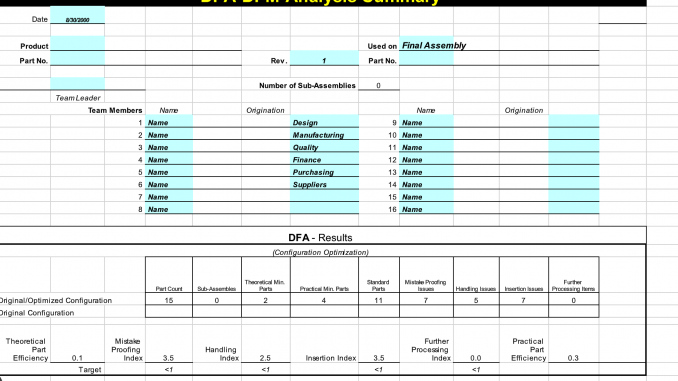
Design for Assembly and Design for Manufacture (DFA-DFM)
Design for Assembly and Design for Manufacture (DFA-DFM) analysis is a crucial component of Six Sigma product development that aims to optimize both manufacturing and assembly processes. At its core, DFA focuses on simplifying assembly by reducing part count and making components easier to handle, while DFM emphasizes creating parts that are simpler and more cost-effective to manufacture.
The DFA approach centers on several key principles: minimizing the number of parts, standardizing components, and reducing assembly steps. Parts should be designed to be self-locating and self-fastening where possible, with built-in error-proofing features that prevent incorrect assembly. This concept, known as “poka-yoke,” ensures that components can only be assembled in the correct orientation.
DFM complements these assembly considerations by focusing on manufacturing efficiency. This includes avoiding complex features that are difficult to machine, using standard materials when possible, and being strategic about tolerance specifications. The approach emphasizes designing parts that can be manufactured without requiring specialized processes or vendors, while ensuring they’re robust enough to withstand handling and processing.
For optimal results, organizations should integrate DFA and DFM considerations early in the design process through cross-functional collaboration. This integration yields multiple benefits: reduced costs, improved product quality, and faster time-to-market. Many companies utilize specialized software tools to evaluate designs against DFA-DFM criteria and maintain continuous feedback loops to incorporate lessons learned from previous projects.
The methodology integrates well with other Six Sigma tools, such as Failure Mode and Effects Analysis (FMEA) and Value Stream Mapping (VSM). While implementing DFA-DFM may face initial resistance and require upfront investment in training and tools, the long-term benefits typically justify these costs. Regular review of outcomes and documentation of lessons learned ensures continuous improvement in the design process.
Success in DFA-DFM implementation requires ongoing training, clear communication of benefits, and a balanced approach that considers both functional requirements and manufacturing efficiency. By viewing product design through the lens of both assembly and manufacturing, organizations can create products that are not only well-designed but also efficient to produce and assemble.
Six Sigma DFA DFM Analysis
Please download the DFA DFM Analysis worksheet (Design For Assembly/Design for Manufacturing) worksheet before going to production with any new prototype. The purpose is to get the design team and manufacturing teams in synch and look for opportunities to simply the product and assembly process. This is a powerful tool and will probably need a Black Belt to help assist the design team at optimizing form, fit, and function
I am very interested in DFA. Can you send this worksheet to me.
Hi Jacky and thank you for the interest. I just emailed you the template.
Thanks,
Jason
I am interested in the template, can you forward it to me as well.
Hi there! I am very interested on DFA. Would you mind sharing it with me?
can i have the template as well?
I am Also Interested in DFM and DFA both. Can you send me both ?