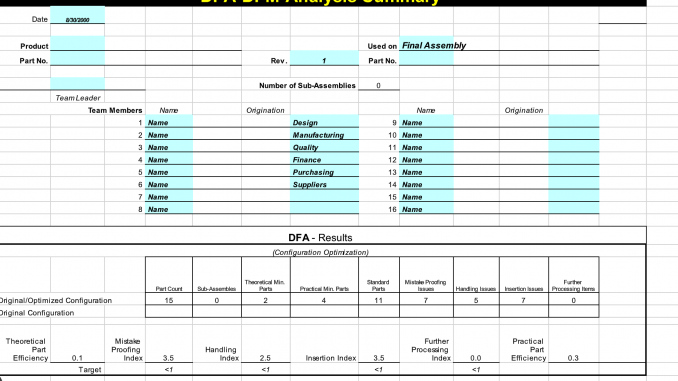
In Six Sigma, the DFA-DFM (Design for Assembly and Design for Manufacture) analysis is an essential part of the product design and development process. The goal of this analysis is to simplify product designs to reduce manufacturing costs, improve quality, and ensure easy assembly. Let’s delve into a detailed breakdown of the DFA-DFM analysis:
Definitions
Design for Assembly (DFA): DFA emphasizes reducing the number of parts, making them easier to handle, orient, and insert, and minimizing the number of assembly steps.
Design for Manufacture (DFM): DFM focuses on simplifying the fabrication of each part to reduce the costs and complexities involved in the manufacturing process.
DFA Analysis
Minimize Part Count: A primary DFA principle is to design products with as few parts as possible. This reduces assembly time, inventory, and simplifies the design.
Standardize Parts: Whenever possible, use standardized parts. This can reduce inventory costs and training requirements.
Minimize Assembly Steps: Reducing the steps to assemble a product decreases labor costs and potential errors.
Error-Proofing: Design parts in such a way that they can be assembled in only one orientation or sequence, minimizing potential assembly errors (also known as “poka-yoke”).
Facilitate Handling: Parts should be easy to pick up, orient, and place without the need for special tools.
Self-Locating Parts: Parts should be designed to easily fit into their required location without force or confusion.
Self-Fastening Parts: Wherever possible, design parts that secure themselves without needing separate fasteners or adhesives.
DFM Analysis
Minimize Complex Features: Overly intricate designs can lead to longer manufacturing times and more potential for defects.
Use Common Materials: Standardizing materials simplifies procurement and can lead to economies of scale.
Design for Efficient Machining: Design features that can be easily machined, avoiding deep pockets or hard-to-reach areas.
Consider Tolerances Carefully: Only specify tight tolerances when absolutely necessary, as they can significantly add to manufacturing costs.
Reduce External Dependencies: Avoid designs that require specialized vendors or processes.
Avoid Fragile Designs: Parts that are thin or have fragile protrusions can be prone to breakage in manufacturing or during handling.
Plan for Testing and Quality Control: Make sure the design includes features or markers that can facilitate easy testing and QC processes.
Integration of DFA and DFM
For optimal results, DFA and DFM should not be viewed in isolation. Instead, they should be integrated into a holistic design approach.
Cross-functional teams, including design engineers, manufacturing engineers, and other stakeholders, should collaborate to ensure that both assembly and manufacturing considerations are integrated into the design process.
Benefits
Reduced Costs: Simplifying designs can lead to significant cost savings in both manufacturing and assembly.
Improved Quality: Simpler designs with fewer parts and easier assembly methods can lead to fewer defects and better final product quality.
Faster Time-to-Market: Simplified designs can shorten production cycles, leading to faster product launches.
Implementation
Many companies use specific DFA/DFM software tools to evaluate and score product designs based on assembly and manufacturing criteria.
Continuous feedback loops, where lessons learned from previous projects are incorporated into new designs, can also be extremely beneficial.
In Six Sigma, DFA-DFM is particularly important because it directly aligns with the methodology’s focus on reducing variability, eliminating waste, and striving for optimal process efficiency.
Be sure to read:
Facilitating Design for Manufacturing by Applying Lean Techniques
Continuous Improvement
As with all Six Sigma methodologies, the goal isn’t just to design efficiently once, but to establish a culture of continuous improvement. Once a product is launched, feedback from the manufacturing and assembly process, as well as from the market, should be gathered and analyzed to make further refinements.
Regularly revisiting and refining DFA/DFM guidelines ensures that they evolve with changes in technology, market demands, and internal company capabilities.
Training and Awareness
Continuous training sessions should be held to ensure that all design and manufacturing engineers are well-versed with DFA/DFM principles.
Design reviews can incorporate DFA/DFM scores or metrics as key criteria, ensuring that designs don’t move forward without considering assembly and manufacturing efficiencies.
Integrate with Other Six Sigma Tools
Failure Mode and Effects Analysis (FMEA): During design, FMEA can be used in tandem with DFA/DFM to predict and evaluate potential failure modes of a design from both a manufacturing and assembly perspective.
Value Stream Mapping (VSM): This tool can help identify waste in the entire product lifecycle, from design to customer delivery. It can spotlight areas where DFA/DFM can be particularly beneficial.
Voice of the Customer (VOC): By understanding customer needs and desires, the design team can focus on essential features and eliminate unnecessary complexities that don’t add value from the customer’s perspective.
Challenges & Overcoming Them
Resistance to Change: Engineers and designers might be resistant to modifying established designs or methodologies. Overcoming this requires clear communication about the benefits of DFA/DFM and illustrating the long-term gains.
Initial Investment: There might be an upfront investment required in terms of training, software tools, or even redesign efforts. However, the ROI in terms of cost savings, quality improvements, and efficiencies typically justifies this investment.
Balancing Aesthetics and Functionality: Especially in consumer-facing products, striking the right balance between an aesthetically pleasing design and one that’s easy to manufacture and assemble can be challenging. Collaboration between design, engineering, and manufacturing teams is key here.
Review and Revision
As products get manufactured and reach the market, a review of the DFA/DFM analysis outcomes should be conducted periodically. Were the predicted savings and efficiencies realized? Were there unforeseen challenges in manufacturing or assembly?
Lessons from each product launch should be documented and incorporated into guidelines for future projects.
In conclusion, the integration of DFA and DFM within the Six Sigma methodology emphasizes the importance of considering the entire product lifecycle, from initial design through to manufacturing, assembly, and customer use. The ultimate goal is to streamline processes, reduce costs, improve quality, and enhance customer satisfaction.