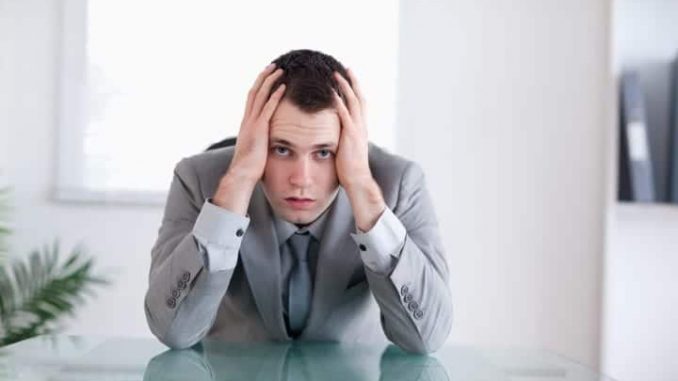
I remember when I had first heard of Six Sigma. 1997. I was enrolled in a management course at Concordia University. During break, outside of the classroom in the corridor, I was talking to a fellow classmate about ISO9001 and its wonders. Keith said, “I know all about ISO 9001, but Six Sigma is the next future.”
I stood curiously as if he was about to reveal one of mankind’s ancient mysteries.
He continues, “ISO just documents your processes. Maybe even your corporate quality objectives. It doesn’t fix anything. ISO only requires that you document your processes, conduct regular audits and process reviews, and record results. It doesn’t cover what to do with the results or handle the data. ISO doesn’t fix anything. It even goes so far as to document the wrong way to perform a process.”
Keith was an aeronautical engineering consultant who was working closely to the manufacturing assembly line.
“Six Sigma will show you how to rally people together to find which opportunities are there to be fixed and how to fix them.”
He was right about ISO and now I just became very interested in this new mystery called Six Sigma.
What is Value?
If you ask anybody, “what is value?” they will almost always answer, “Something that creates value.” Obviously. But what does value mean?
Value is a concept that requires a context. For example, for a corporation, it means creating share-value, which means higher dividend payouts, increased market share but to name a few.
For a manufacturing context, creating value may imply lower costs of raw materials that go into the finished product. Or it can mean lower manufacturing cycles or Takt time.
For a logistics context, higher value may mean lower shipping costs, fewer freight damage, claims, etc.
In any case, value, at the end of the day, will likely translate into better profit margins. This doesn’t necessarily mean increasing revenue. If you keep the revenue flat, but you reduce your costs (fixed, variable, overhead, etc.), profit margins will increase, right?
Value is a concept that is not necessarily based in Six Sigma, but introduced by Lean Manufacturing. Lean thinking goes so far as to say that eliminating any of the 7 wastes increases value to the customer.
When a customer purchases your products or services, they expect the product to do as stated. Any unwanted or buggy, not-working feature does not want to pay for something that doesn’t bring them added value.
For Six Sigma to work, you’ve got to identify the value it will bring to the project. This clearly has to be seen in the project’s charter. The charter should state a problem, and steps to resolve the problem or reduce the occurrences of the problem. Ultimately, there will be a defined, measurable end goal such as, “reducing X by Y$”, or “increasing A efficiency from 81% to 95% in X time”, or “better qualifying supplier selection and raw material component costs to reduce overall COGS by 17% in Z months.”
What Problem Are You Trying to Solve? Is There Really a Problem?
A Six Sigma Black Belt can identify opportunities easily. There is never a shortage of problems or processes that can be improved. Some problems that require fixing will reap more benefits or value to a company, while others less. However, the bigger problems may require much more effort.
Depending on the size of a company, you may get much more resistance, or push-back, from key stakeholders. From my experience, small to mid-sized companies, generally those under 100 employees will show much more resistance to change than working in large, multi-national companies
But where to start? It’s smart to start with the low hanging fruit. Or internal Voice of the Customer (VOC) interview or focus groups with employees involved or affected by a particular problem.
Once you identify a problem to improve, define the project charter, get executive sponsorship, be careful not to be too proud. You may soon find out that a particular sub-par supplier may have a strong personal relationship or family relationship with an executive. This will be difficult to fix. Go to the next problem or meet with your executive to discuss the best next steps. Perhaps your executive will help you communicate with the supplier and all parties will work in collaboration. Maybe your executive will want to leave things unchanged and let his relationship flourish with his incestuous supplier. This will usually be the case.
Is Six Sigma Already in the Work Place?
What I’ve learned about 6S in the work place is that there must already be a culture of quality and wanting to make things better. Many employees couldn’t care less as long as they get a bi-weekly pay deposit.
Introducing Lean Six Sigma at work when nobody knows barely more than ISO 9001 will be daunting. What they don’t teach you when you were getting certified is that company cultures are usually the most difficult barrier to overcome. Many employees, from Millennials to seasoned professionals, don’t like to be told how to do something better or that they are producing defects or even waste.
Starting a new career at a company, where there is already a continuous improvement or operational excellence (OpEx) department may say a lot about your current employer.
I don’t know anyone who thoroughly enjoys being embarrassed in a meeting room surrounded by other colleagues and peers over flawed data but I know that doing so continuously will get you ousted from any social circles you have at work. Trying to institute a Six Sigma vision at your work place, while probably a great idea, will always be difficult.
If your current boss didn’t hire you for your abilities at Six Sigma, then tell yourself any initiative you try to inspire in him, will be
Why Six Sigma May Backfire on You
In the Measure phase of DMAIC, the black belt project champion will have to collect data which he or she doesn’t already have. As Six Sigma is simply about transforming a practical problem into a statistical one, then finding a statistical solution to be applied as practical solution, much of the data collected will highlight flaws produced by a given process, usually ultimately always pointing to a human. But we don’t like to be embarrassed.
Finding too many opportunities for improvement may alienate you from your colleagues at the lunch table, but it may be the right approach in more mature, larger scaled organizations.
To Wrap Things Up
Closing up, Six Sigma in the workplace can produce very effective results. This is true for Lean manufacturing or both DMAIC and DFSS approaches to Six Sigma, as long as you are asked to prepare a project with forecasted savings.
Wait to be asked what Six Sigma can do to your company rather than tell your company what Six Sigma can do for its stakeholders.
Be the first to comment