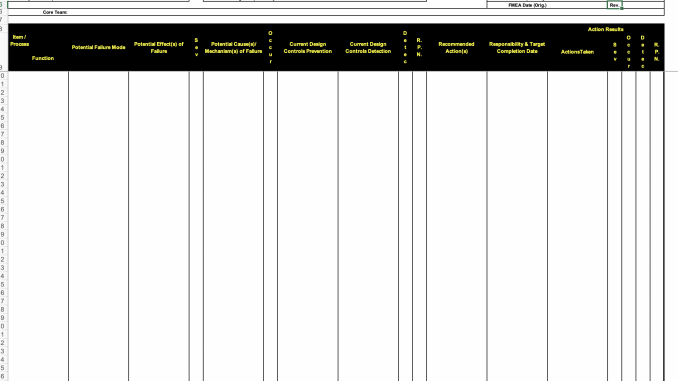
Failure Mode Effects Analysis – FMEA Template
The Failure Mode Effects Analysis is a great tool used in the Aerospace industry since the 1960s and still in use today for DFM (Design For Manufacturing) in Lean manufacturing environments. Use our FMEA Template to
- Identifying the ways in which a product can fail
- Estimating the risk associated with each failure mode
- Rank ordering the failure modes to prioritize the design teams efforts
- Track corrective actions and provide a permanent record for subsequent design and process FMEAs
The main goal of the template is to identify ways that a product can fail and take action to remove the failure modes before they occur.
Role of the FMEA Template
- Key tool of the design team to improve the product in a preemptive manner (before failures occur)
- Used to prioritize resources to insure product development efforts are beneficial to customer
- Used to document completion of projects
- Should be a dynamic document, continually reviewed, amended, updated
- Should serve as starting-point for future DFMEA’s of similar products.
- Is the catalyst of Process FMEA’s.
Uses for templatestaff’s Template
System
- Used to analyze failures of the end product in a customers system
- Focuses on potential failure modes associated with the functions of the end product
Functional
- Used to analyze systems and sub-systems of the product in the early concept and design stages
- Focuses on potential failure modes associated with the functions of each system and sub-system
Component / Material
- Used to analyze systems and sub-systems down to the fundamental components and materials used in the design
- Focuses on Components and Material
Process
- Used to analyze manufacturing and assembly processes
- Focuses on Process Inputs
How is a Design FMEA different from a Process FMEA?
The Design FMEA assumes that the process is in control and capable of meeting the process spreads used in the design. It also assumes that material, and components are performing as specified in the design documentation.
Failures can be caused by:
- Unclear specifications
- Inadequate knowledge of environmental conditions
- Insufficient Analysis, Modelling and Simulation
- Poor Design
- Insufficient Testing
- Not designing for process requirements
Controls are related to the design process:
- Prevention – Analysis, Simulation and Modelling
- Detection – Prototype Testing, Design Verification Testing, Reliability Testing
The Process FMEA assumes that the design is capable and focuses on process capability and control.
EDITOR’S UPDATE
No tool comes as close as the FMEA when it comes time to prioritize which issues need to be resolved first.
As a result of the FMEA, often encouraged to be preceded by the Ishikawa (fish-bone), and C&E Matrix (Cause & Effect), the RPN (Risk Priority Number) is derived. This is the product of Importance x Severity x Occurrence (you need to see this in the template firsthand so don’t hesitate!)
Be the first to comment