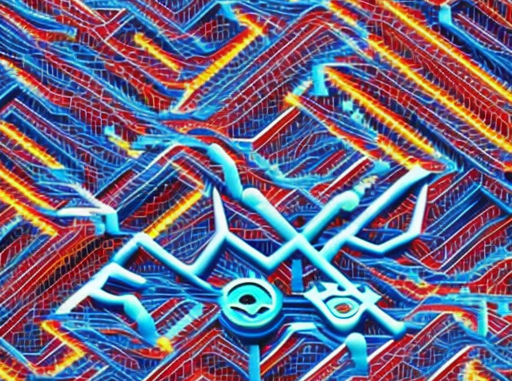
Implementing Six Sigma in the context of Industry 4.0 involves using data-driven methodologies and advanced technologies to improve processes, reduce defects, and enhance overall quality and efficiency. Here’s a detailed example of how Six Sigma can be applied in an Industry 4.0 setting:
Problem Statement: Let’s say you work for a manufacturing company that produces electronic components. The company has identified a recurring issue with the soldering process that results in defects and increased rework, leading to higher production costs and decreased customer satisfaction. The goal is to reduce defects in the soldering process.
Step 1: Define (DMAIC Phase 1)
Project Charter: Create a project charter that outlines the problem, goals, team members, scope, and timeline. It should also define the key performance metrics, such as defect rate and customer satisfaction score.
Voice of the Customer (VOC): Gather feedback from customers regarding their expectations and requirements for the electronic components’ quality.
Step 2: Measure (DMAIC Phase 2)
Data Collection: Collect data from various sources within the manufacturing process. In Industry 4.0, you can use IoT devices, sensors, and automation systems to gather real-time data on temperature, humidity, soldering machine performance, and defect rates.
Data Analysis: Use statistical tools and software to analyze the collected data. Identify the root causes of defects, potential sources of variation, and key process parameters affecting soldering quality.
Step 3: Analyze (DMAIC Phase 3)
Root Cause Analysis: Utilize advanced analytics and machine learning algorithms to pinpoint the primary causes of defects. This might involve analyzing historical data to uncover patterns and correlations.
Hypothesis Testing: Develop and test hypotheses to validate the root causes. Industry 4.0 technologies can help you perform complex simulations and predictive modeling to understand the impact of different variables on soldering quality.
Step 4: Improve (DMAIC Phase 4)
Optimization: Use simulation and optimization tools to find the ideal process parameters that minimize defects and improve soldering quality. This may involve adjusting machine settings, fine-tuning temperature and humidity control, or upgrading equipment.
Automation: Implement automation solutions, such as robotic soldering or automated quality inspections, to reduce human error and increase consistency in the soldering process.
Step 5: Control (DMAIC Phase 5)
Statistical Process Control (SPC): Implement SPC tools and IoT devices to monitor the soldering process in real time. Set up control charts and alarms to detect any deviations from the optimized process.
Documentation and Standardization: Document the new standard operating procedures and ensure that all operators are trained to follow them consistently. Use digital documentation and training tools enabled by Industry 4.0 technologies.
Step 6: Verify and Sustain (DMAIC Phase 6)
Performance Metrics: Continuously monitor and measure the performance metrics defined in the project charter. Ensure that defects remain reduced, and customer satisfaction remains high.
Feedback Loop: Use feedback from customers, operators, and IoT sensors to make continuous improvements. Machine learning models can help predict potential issues before they occur.
Knowledge Sharing: Promote knowledge sharing among team members and departments, and use digital platforms and collaborative tools to facilitate communication and data sharing.
By implementing Six Sigma in an Industry 4.0 environment, you can not only solve specific problems but also create a culture of data-driven decision-making and continuous improvement throughout the organization. This approach leverages the power of advanced technologies and analytics to drive quality and efficiency improvements.
Step 7: Scale and Expand
Replication: If the initial Six Sigma project yields significant improvements in the soldering process, consider replicating the approach in other areas of your manufacturing operations where similar issues may exist.
Cross-Functional Collaboration: Encourage collaboration between different departments and teams, including engineering, production, quality control, and IT. Share best practices and lessons learned to optimize processes across the organization.
Step 8: Continuous Learning and Adaptation
Data Analytics and AI: Leverage artificial intelligence and machine learning to continuously analyze data from sensors and IoT devices. These technologies can help in predicting defects or process deviations, allowing for proactive intervention.
Blockchain for Traceability: In an Industry 4.0 setting, blockchain technology can be used for traceability and transparency. You can record critical process data on a blockchain to ensure data integrity and traceability of components throughout their lifecycle.
Advanced Robotics: As technology advances, explore the use of advanced robotics for more intricate and delicate soldering tasks. Collaborative robots (cobots) can work alongside human operators, improving precision and efficiency.
Digital Twins: Develop digital twins of your manufacturing processes. These digital representations allow you to simulate and optimize processes in a virtual environment before implementing changes in the physical world, reducing risks and costs.
Step 9: Integration with Supply Chain and Customers
1. Supply Chain Optimization: Collaborate with suppliers to optimize the supply chain. Industry 4.0 technologies like IoT and blockchain can enhance transparency and traceability in the supply chain, reducing the risk of receiving subpar materials.
Customer Feedback Loop: Continue gathering customer feedback and integrate it into your continuous improvement process. Use digital platforms to collect and analyze customer feedback in real time.
Step 10: Compliance and Certification
Regulatory Compliance: Ensure that your processes meet industry-specific regulations and standards. Industry 4.0 technologies can help automate compliance monitoring and reporting.
Certifications: Pursue relevant certifications such as ISO 9001 (Quality Management) or ISO 13485 (Medical Devices) to demonstrate your commitment to quality and process improvement.
Step 11: Employee Training and Development
Digital Skills: Invest in training programs to equip your workforce with the digital skills required to operate and maintain Industry 4.0 technologies effectively.Change Management: Implement change management strategies to ensure employees embrace the cultural shift toward data-driven decision-making and continuous improvement.
Step 12: Performance Review and Benchmarking
Performance Metrics: Regularly review and update your performance metrics. Benchmark your processes against industry leaders and identify areas for further improvement.
Innovation: Encourage a culture of innovation by providing incentives for employees to suggest and implement process improvements using the latest Industry 4.0 technologies.
By following these additional steps and integrating Industry 4.0 technologies into your Six Sigma implementation, you can create a robust framework for continuous improvement and innovation. This approach not only addresses specific issues but also positions your organization to thrive in the era of smart manufacturing and digital transformation.
Step 13: Predictive Maintenance and Asset Management
IoT-Based Predictive Maintenance: Implement IoT sensors and predictive maintenance algorithms to monitor the health of manufacturing equipment. This allows you to detect potential issues before they lead to downtime or defects, optimizing asset utilization.
2. Digital Asset Twins: Create digital twins of your manufacturing equipment. These virtual representations enable real-time monitoring of equipment performance, helping you make data-driven decisions regarding maintenance and upgrades.
Step 14: Energy Efficiency and Sustainability
Energy Monitoring: Utilize Industry 4.0 technologies to monitor energy consumption in your manufacturing processes. Implement energy-efficient practices and technologies, reducing your environmental footprint and operational costs.
Sustainability Initiatives: Incorporate sustainability goals into your Six Sigma projects. For instance, redesign products and processes to minimize waste, and explore the use of recycled or eco-friendly materials.
Step 15: Cybersecurity and Data Protection
Data Security: Ensure the security of your data, especially when using IoT devices and cloud-based solutions. Implement robust cybersecurity measures to protect sensitive information from cyber threats.
Data Governance: Establish data governance frameworks to maintain data integrity and compliance with data privacy regulations (e.g., GDPR). Ensure that only authorized personnel can access and modify critical data.
Step 16: Supply Chain Visibility and Resilience
End-to-End Visibility: Leverage Industry 4.0 technologies such as blockchain and RFID to achieve end-to-end supply chain visibility. This allows you to track the movement of materials and components in real time.
Supply Chain Resilience: Develop strategies to enhance supply chain resilience, enabling your organization to respond effectively to disruptions such as natural disasters, geopolitical events, or supply chain interruptions.
Step 17: Human-Machine Collaboration and Augmentation
Augmented Reality (AR) and Virtual Reality (VR): Implement AR and VR technologies to provide workers with real-time instructions and support during complex tasks. This enhances worker productivity and reduces errors.
Cobotics: Further explore the use of cobots (collaborative robots) that can work alongside human operators. Cobots can handle repetitive and physically demanding tasks, allowing human workers to focus on more complex and value-added activities.
Step 18: Data-Driven Decision-Making
Advanced Analytics: Continuously invest in advanced analytics capabilities to extract meaningful insights from your data. This includes the use of machine learning, natural language processing, and big data analytics to make data-driven decisions.
Real-time Dashboards: Develop real-time dashboards and reporting tools that provide instant access to critical performance metrics. These dashboards enable quick responses to deviations and facilitate proactive decision-making.
Step 19: Continuous Improvement Culture
Employee Empowerment: Empower employees at all levels to contribute to process improvement. Establish a culture where employees feel encouraged to identify and report issues and suggest improvements.
Kaizen Events: Organize regular Kaizen events or improvement workshops where cross-functional teams brainstorm and implement small-scale improvements. Use digital collaboration tools to facilitate these events.
Step 20: Certification and Recognition
Six Sigma Certification: Encourage employees to pursue Six Sigma certifications to deepen their knowledge and expertise in process improvement methodologies.
Recognition Programs: Implement recognition programs to acknowledge and reward employees and teams for their contributions to quality improvement and innovation.
In conclusion, the successful implementation of Six Sigma in an Industry 4.0 environment is a dynamic and evolving process. It requires a holistic approach that combines data-driven methodologies, advanced technologies, and a culture of continuous improvement. By following these additional steps and embracing the opportunities presented by Industry 4.0, organizations can not only solve immediate problems but also position themselves as leaders in their industries, delivering high-quality products while remaining agile and competitive in an increasingly digital and interconnected world.
Be the first to comment