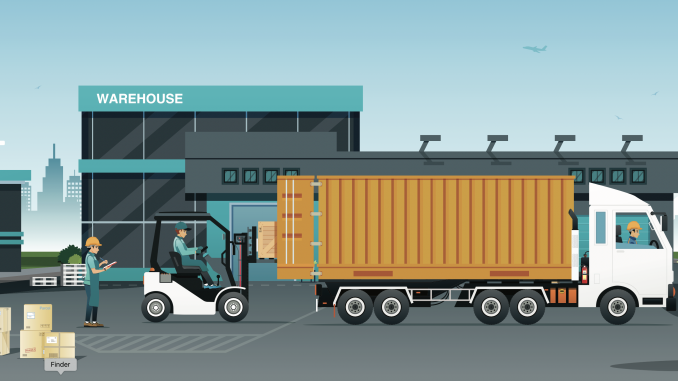
Here’s a basic Workplace Safety Manual that you can copy/paste into Microsoft Word (or Google Workspace Docs) to get you going quickly. This template has been adapted for an X-Ray manufacturing company but you can adapt it to your company’s needs. Also, note that there are no provisions (you’ll have to add your own) for COVID-19 physical distancing in the workplace.
Workplace Safety Manual
<COMPANY NAME>
<company address>
Table of Contents
- Introduction
- Company Responsibilities
- Employee Responsibilities
- Visitors
- Contractors and Suppliers
- Hazard Identification and Control (Prevention)
- Best Practices
- Personal Protective Equipment (PPE)
- Equipment Operation
- What to do in case of a workplace accident
- In case of medical emergency
- In case of fire
- Emergency Response Plan
- Material and Equipment Storage
- Responsible Waste Disposal
Revisions
Indicate approved document revisions and history here.
Introduction
This manual provides general guidelines for integrating workplace health and safety at <COMPANY NAME>.
We hope this guide, written in plain, non-technical language will assist in the prevention of workplace injuries and the promotion of a safe working environment.
<COMPANY NAME>’s Responsibilities
- Fostering a workplace safety culture in which employees and their supervisors work together to ensure workplace safety;
- Establishing administrative procedures that encourage employees to report unsafe conditions and unsafe practices to their supervisors
- Ensuring that the health and safety policies and procedures conform with the requirements of the Commission des normes, de l’équité, de la santé et sécurité au travail (CNESST) (if the company is based in Quebec, Canada)
- Establishing procedures for enforcing company safety rules;
- Maintaining records of injuries, illnesses and workers’ compensation;
- Coordinating first aid training and the provision of first aid to employees;
- Providing advice to employees and the employer in matters of occupational health and safety
- Organizing a workplace safety committee to meet quarterly. For this, two employee representatives are required per address
Employee Responsibilities
The primary responsibility of any <COMPANY NAME> employee is to perform his or her duties in a safe manner to prevent injury to themselves and others. The following safety procedures are established to help you stay safe and injury free. Violation of the above rules, or conduct that does not meet minimum accepted work standards, will result in discipline, up to and including discharge.
All employees are required to comply with the safety requirements outlined in this manual, as well as any which may be required when visiting customer or supplier premises.
All employees are required to work in a manner that reflects positively on the company.
As a condition of employment, employees MUST become familiar with, observe, and obey <COMPANY NAME>’S rules and established policies for health, safety, and preventing injuries while at work.
In accordance to the Commission des normes, de l’équité, de la santé et sécurité au travail (CNESST) NO EMPLOYEE IS EVER REQUIRED to perform work that he or she reasonably believes is unsafe, or that he or she think is likely to cause injury or a health risk to themselves or others.
If an employee has any questions about how a task should be done safely, he or she is under instruction NOT to begin the task until he or she discusses the situation with his or her supervisor. Together, they will determine the safe way to do the job.
Employees of <Company Name> are required to follow all client/suppliers’ safety and security procedures during their visits and the same applies when receiving visitors at <Company Name>
If the client/supplier host does not advise you regarding safety hazards, ensure you have identified the emergency exit locations.
Keep your eye on the path you are working and avoid any tripping/slipping hazards. When on stairs maintain three-point contact (hand on rail and feet on stairs);
If you will be touring a factory, dress appropriately. Wear your safety shoes and bring your safety glasses. Avoid clothing that is either constructive or too loose; loose clothing may get caught in machinery or other equipment.
You are responsible to keep your work area clean and safe. Clean-up throughout the day, disposing of trash and waste in approved containers, wiping up any drips, spills immediately, and putting equipment and tools away as you are finished with them.
Visitor, Contractors, and Suppliers
Al must adhere to the safety guidelines within this manual, especially within designated zones
Hazard Identification and Control (Prevention)
Hazard Identification and Control are key components in maintaining a safe and healthy workplace. Health hazards, occupational factors or illnesses, arising in and from the workplace, which may cause impaired health and well being, sickness, or significant discomfort and inefficiency must be identified, monitored, and controlled.
Report any unsafe conditions or situations to your supervisor. If you have suggestions on improving any aspect of safety in the facility, discuss it. If you are unsure of how to operate a piece of equipment or complete and assignment, ask for help. Asking for help when you are unsure reduces the chance of injury.
Best Practices
Special attention must be given to maintaining clear walkways and roadways. Removal of trash, slipping and tripping hazards, and proper storage of materials is an ongoing requirement.
Office Safety
Following are general, common-sense rules for ensuring office safety:
- Never leave file drawers open, or open multiple file drawers at once
- Do not stack heavy or bulky objects on top of cabinets
- Do not store frequently used objects above shoulder height or below knee height.
- Never reach into office machines without turning them off and unplugging them if possible.
- Keep your work area free to trip hazards such as storage in walkways, cords across aisles, and damaged floor coverings.
- Inspect step stools/ladders before use. Be sure to keep a stationary object in front of you when using a step stood to provide stability.
Never use defective or broken equipment. Report these problems to your supervisor.
Heavy Lifting
Back injury is the leading cause of lost time injuries. Experience and statistics have shown prevention programs significantly reduce the incidence of back injuries. Below are a few basic suggestions to lifting that may prevent the occurrence of a back injury.
- Avoid lifting where possible and practical by pushing, pulling, rolling or sliding the object to be moved.
- Use mechanical aids (hand trucks, carts, winches, forklifts, etc.)
- Request help from other employees when necessary, particularly when you find yourself in a difficult or awkward lifting situation.
When lifting heavy objects from the floor or ground can’t be avoided, here are some basic principles to prevent back pain and injury:
- Plan the lift (P.S.I)
- Lift only loads you can safely handle.
- Establish good footing.
- Keep the load close to the body.
- Bend at the knees as you grasp it and keep your eyes looking straight ahead.
- Get a full handgrip and keep your body erect.
- Lift smoothly by straightening the legs (avoid jerky or snatching lifts).
- Avoid the lift and twist action. When turning, shift the position of your feet rather than twisting your body at the waist.
- Reverse the procedure to set the object down.
- If you need help moving material, ask for help.
When you lift, use your leg muscles by squatting close to the load, preserving the curve in your back, spreading your feet, and lifting with your legs, keeping the load close to your body.
When you turn holding an object, move your feet and do not twist.
Using Ladders
- Inspect all ladders prior to each use;
- Ladders must be placed on secure footing;
- Only one person is allowed on a ladder at a time;
- Never stand on the top two steps of a stepladder;
- Always maintain 3-point contact when working on ladders;
- Never reach beyond arm length when working on a ladder; and
- Never use metal ladders when working on or around electrical equipment.
Electrical Safety
All electrical cords and cables if practicable must be elevated or covered to protect them from damage and to mitigate tripping hazards.
Qualified electricians are the only personnel authorized to repair electrical equipment. Field repairs or tampering with any electrical equipment by unauthorized personnel will not be tolerated.
- Never operate or tamper with the electrical main switch or breakers
- Report all electrical problems and suspected problems to your supervisor
- Inspect all plugs, chords, and portable equipment prior to use
- Report any damaged electrical equipment to your supervisor
- Extension cords are to be used only for temporary applications. Never stretch cords across aisles or areas where others may trip over them
- Remove any power or extension cords, which are missing the ground prong
Radiation Safety
While X-Ray radiation can be dangerous, it is safe to work at <COMPANY NAME>. Much effort has been put in place to ensure safeguards for employees working with the possibility of being exposed to X-ray radiation.
Specialized training will be provided to employees in the manufacturing facility and no harm will arise for those respecting the specialized safety guidelines.
It must be noted that during an X-Ray scan (while the diffusers illuminate red), care must be taken that you are at least 2 m away from the scanner shrouds and while a scanned item displaces the lead curtains upon entry or exit of the scan tunnel.
Handling Lead
Lead is used in many industries today and is deemed safe. The dangers from lead arise from ingesting it.
Some employees may be required to work with lead. When working with lead, work gloves, safety glasses, as well as safety glasses must be worn at all times.
Personal Protective Equipment (PPE)
The purpose of personal protective equipment (PPE) is to provide an effective barrier between a worker and potentially dangerous objects, substances, and processes.
Safety Glasses
- All personnel must wear properly fitting eye and face protection
- Face and eye protection shall be kept clean and in good repair.
- If a worker cannot wear safety glasses, as documented by a physician’s note, alternate arrangements must be made to verify the individual’s face and eyes are protected.
- All components of prescription glasses that are being used for eye protection must meet approved applicable regulatory standards.
- The prescription glasses will include side-shields that must meet the applicable regulatory standards. Coverall glasses or goggles shall be required for prescription glasses that do not meet the standard.
- Face shields are required when grinding/cutting steel, concrete, chemical use.
- When using a face shield, safety glasses are also required under the face shield.
Safety Shoes
- All personnel at <COMPANY NAME> manufacturing & warehouse premises must wear CSA approved safety footwear.
- Safety footwear must be in good repair. It is the responsibility of the employee to verify that their footwear is in proper working condition.
Work Gloves
All personnel must have appropriate gloves available for their task on their persons. Gloves are to be worn when conducting work activities with hazards that may cause injury to hands.
Radiation Aprons, Throat Guards, Masks, and Gloves
For those employees working in the manufacturing facility, specifically performing X-Ray tube seasoning, as well as testing the X-Ray sources for alignment and image quality, these PPEs must be worn at all times.
Personal Dosimeter
While <COMPANY NAME>’s products are safe, Heath Canada requires that employees working closely with the manufacturing of X-Ray equipment, that personal dosimeters be supplied. These personal dosimeters are provided by Health Canada and must be returned periodically to ensure your safety with respect to maximum allowable levels of X-Ray radiation.
Equipment Operation
Hand and Power Tools
All employees using hand/power tools are to inspect these tools before use to ensure they are in a safe operating condition. Ensure all guards are in place and operational (i.e. grinder guard and second handle in place).
All tools requiring repair or missing guards must be immediately removed from service and reported to your supervisor. Such tools will be taken out of service, tagged and repaired before making them available to any other worker.
Only hand tools that are in good condition and that are the right tool for the job should be used.
Pallet Jacks (jiggers)
Pallet jacks are designed for smooth surfaces and are difficult to maneuver on uneven surfaces or in areas with debris.
- Before using a pallet jack, always ensure the controls are undamaged and responsive
- Always plan your journey before jumping straight into using the pallet jack
- Never carry riders or ride the equipment yourself
- No horseplay, it can cause serious injuries!
- Never place your feet under a pallet jack
- Feet, hands or any body part should never be placed underneath a pallet
- Use proper lifting techniques loading/unloading and operating the pallet jack
- Park the pallet jack in a level place, forks lowered
- Don’t block exits or emergency equipment, i.e. fire extinguishers
- Do not leave a pallet jack unattended and elevated
- Put pallet jacks safely away in a predetermined storage location when not in use with the handle raised and locked
- Keep the jack out of a traffic area, avoid a tripping hazard
- Always let pallet jack down when stocking product or anytime the pallet jack is left unattended
Forklift
Only trained employees with the proper license operate the forklift. While operating any equipment, you will comply with all applicable laws and will not operate the equipment while under the influence of drugs or alcohol, not after taking prescription or over the counter medications that may interfere with the safe operation of the equipment.
In the specific case of forklifts, you will not:
- Drive forklift trucks up to anyone standing in front of a bench or other fixed object.
- Run over loose objects on the roadway surface.
- Allow persons to stand or pass under the elevated portion of any truck, whether loaded or empty.
- Allow any person to ride on forklift trucks except the operator, unless the forklift truck has provisions for passengers.
- Place arms or legs between the uprights of the mast or outside the running lines of the truck.
- Use forklift truck for opening or closing freight doors.
- Block fire aisles, access to stairways, or fire equipment with the forklift truck or the load being handled.
- Participate in stunt driving or horseplay.
Forklift Fuel Tanks
All propane tanks must be secured outdoors under lock and key to prevent theft.
What to do in case of a workplace accident
In accordance with the CNESST, all work-related injuries must be reported to Human Resources immediately.
Failure to immediately report injuries can result in loss of Worker’s Compensation benefits. After each medical appointment resulting from a work-related injury, you must contact your supervisor to discuss your progress. You must also give your supervisor any paperwork that you received at the appointment.
In case of a medical emergency
- Upon discovering a medical emergency, call 911.
- Stay with the person involved being careful not to come into contact with any bodily fluids, unless properly trained and equipped.
- Send someone to the building entrance to greet the first responders.
- Often two fire department units will arrive, so the second greeter should wait at the entrance to receive the second unit while the first greeter escorts the fire dept. personnel to the scene).
Employees in the immediate vicinity of the emergency, but not directly involved, should leave the area.
Human Resources will make any necessary notification to family members of the person suffering the medical emergency.
In case of fire
Fire extinguishers must always be available and must not be covered or blocked by materials or debris. Clear access to fire protection equipment must be maintained at all times.
In case of fire:
- Activate a fire alarm and tell someone to call 911
- If you have received fire extinguisher training, you can decide to use a fire extinguisher following these instructions
- on becoming aware of a fire alarm, employees should immediately evacuate the building according to the emergency response plan.
- Do not delay evacuation to get personal belongings or to wait for co-workers. Also, all doors should be closed as the last person passes through.
- Supervisors should be the last persons to leave the area. Check in conference rooms, lunch room, lavatories, and offices to be sure that all personnel have evacuated.
- Upon exiting the building, personnel should report to a manager for a headcount.
- If any employee is missing, an immediate report should be made to the site manager who will in turn report to the first available fire department officer.
- Employees should stay together in a group at the emergency meeting point until further notice
- The order to re-occupy the building will be issued by Human Resources or the
Emergency Response Plan
- In the event of any serious injury or fire, call 911. Send someone to the facility entrance to meet the First Responders. If in doubt, call 911.
- Upon discovering a fire, alert others in immediate danger and initiate facility wide fire alarm.
- When the evacuation signal is given, all employees should immediately turn off equipment, close doors, and evacuate to their designated evacuation areas. Attendance will be taken to account for all personnel. Stay together in the group until further instructions are received.
- Do not attempt to fight any fire which is uncontained, too hot, too smoky, or if you are too frightened.
- Do not touch blood or any other bodily fluid during or following an incident. If you are trained to administer first aid, gloves and other barriers are located with the first aid equipment. If you think that you have been exposed to bodily fluid, notify your supervisor immediately.
Meeting Point
Emergency meeting points are a predetermined location where a designate will be sent to meet responding emergency response crews.
- For the office, the meeting point is at the entrance of the parking lot on Route Trans Canada
- For the manufacturing facility, the meeting point is at the entrance of the parking lot on Delmar
Emergency Contact List
As part of the emergency response plan, the site will complete an Emergency Contact List that shall be kept current, including the following information and contacts:
Coordination
All employees must be able to respond to, and participate in, any emergencies that may occur. All subcontractors/trade contractors should participate by identifying their qualified first aid personnel. The main responsibility during an emergency coordination is to respond to the call for emergency help.
Material and Equipment Storage
All materials must be properly stacked and secured to prevent sliding, falling or collapse. Aisles, stairs and passageways must be kept clear to provide for the safe movement of personnel and equipment and to provide access/egress in an emergency.
To protect the other parties, tools and equipment are never to be left unattended. Always store tools and equipment (unless flammable, corrosive, or explosive) within a designated storage area or a construction area.
Material Safety Data Sheets
All chemical products used in production must have an accompanying Material Safety Data Sheet (MSDS) available near its storage cabinet.
Responsible Waste Disposal
Wherever possible <COMPANY NAME> will minimize production of non-hazardous waste through recycling, reuse, and waste minimization initiatives.
However, some products require special disposal.
Please use the designated waste bins for battery disposal.
For chemical products found in the manufacturing facility such as paints, adhesives, grease & lubricants, and lead, please store in designated quarantine area and let your supervisor know so that proper containment and disposal can be delegated to specialized recycling and disposal firms.
Never mix chemical products together.